Engineering Project Documentation
Engineering Project Documentation
The quality of the design and documentation produced has a major influence on the overall performance and efficiency of production projects. Designers provide the basic blueprints for representing the ideas and concepts that manufacturers need to make products a reality. However, it is the quality of the documentation provided which determines how effective and efficient turn around time is for production. Inadequate and deficient design and documentation impacts the production process efficiency by leading to delays, rework and variations, contributing to increases in project time and cost. But, there are levels before manufacturing can happen that can delay this process, or even bring production to a halt. There are a countless number of documentation used throughout every company. They can range from quality assurance to manufacturing. Without running through a complete list of all the documentation that a company would use, we will instead sum the documentation into several categories below.
❖ Management documentation.
❖ Quality assurance.
❖ Engineering documentation.
❖ Fabrication, Assembly, Test, and Installation documents.
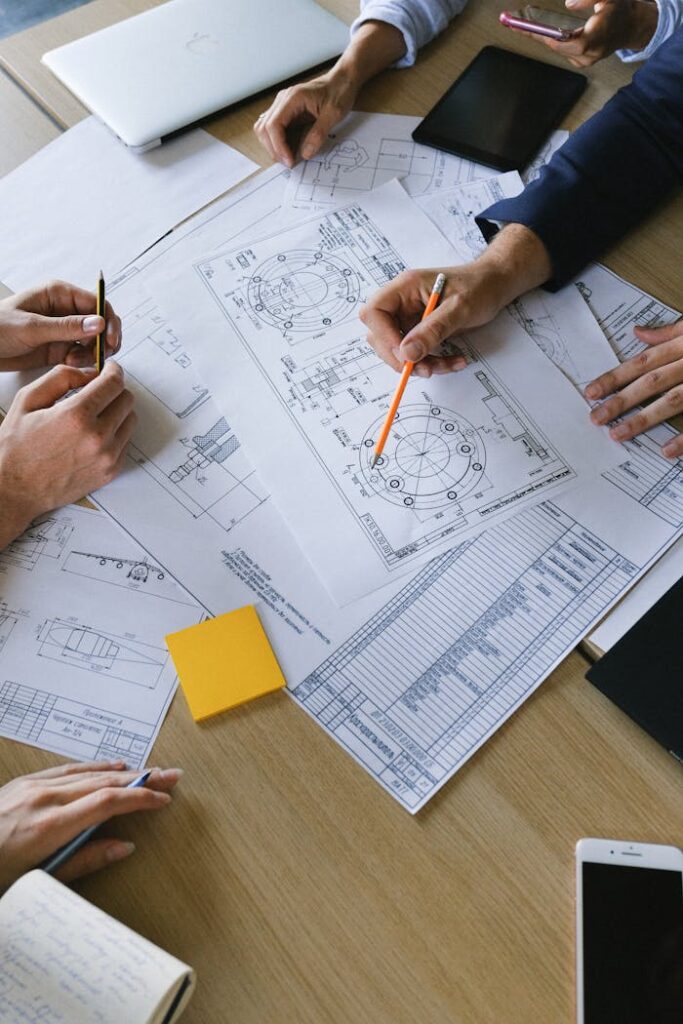
1.Management Documentation
Management documentation is the process of managing and controlling an organization’s documents, including their creation, modification, approval, and accessibility. Document management can be done manually or with a document management system (DMS).
A DMS can help organizations: Increase transparency: Ensure that everyone is working with the same information Securely share
content: Store documents in a secure location and share them for a limited time
Mitigate risk: Ensure that key technical information remains available even when employees leave
Improve sales: Capture leads with web forms and store sales and marketing material in a digital repository Some features of a DMS include.
Security: Access control and editing rights to protect sensitive information
Storage: Virtually unlimited storage space
Search and retrieval: Easy indexing for search and retrieval
Collaboration: Multiple users can work on documents at the same time
Version control: Monitor change and validity over time
2. Quality Assurance
Quality assurance (QA) is any systematic process of determining whether a product or service meets specified requirements.
QA establishes and maintains set requirements for developing or manufacturing reliable products
Failure testing: Failure testing continually tests a product to determine if it breaks or fails. For physical products that need to withstand stress, this could involve testing the product under heat, pressure or vibration. For software products, failure testing might involve placing the software under high usage or load conditions.
Statistical process control (SPC): SPC is a methodology based on objective data and analysis and developed by Walter Shewhart at Western Electric Company and Bell Telephone Laboratories in the 1920’s and 1930’s. This methodology uses statistical methods to manage and control the production of products.
Total quality management: TQM, which applies quantitative methods as the basis for continuous improvement. TQM relies on facts, data and analysis to support product planning and performance reviews
3. Engineering Documentation
Engineering documentation is a detailed record of a product’s design, development, and implementation process. It can include:
Design specifications
Technical drawings and schematics
Calculations and analysis reports
Test plans and results
Material lists and sourcing information
Engineering documentation is used to justify engineering development and describe the work that needs to be done. It can also be used to maintain and enhance software
Engineering documentation is the set of drawings, specifications, calculations, and instructions that describe the design, fabrication, testing, and operation of a part or system. It helps you communicate your ideas, ensure quality and consistency, and comply with standards and regulations
4. Fabrication
the act of making something (a product) from raw materials. “the synthesis and fabrication of single crystals” synonyms: manufacture, manufacturing.
Fabrication is using processes to create component parts that can be used to make a product or structure, as well as the process of constructing an item from standardized parts. Manufacturing, meanwhile, is the processing of raw materials into a finished product that can be sold to a consume
5. Assembly
Engineering documentation for assembly includes drawings, specifications, calculations, and instructions that describe the design, fabrication, testing, and operation of a product. Assembly documentation is a type of engineering documentation that provides detailed instructions for assembling a product.
Here are some examples of engineering documentation:
Assembly drawings: A graphical representation of the product or assembly, with leader lines pointing to each component. It may also include notes, a table of materials, and step numbers.
Design specifications: A component of engineering documentation that describes the design of a product.
Calculations and analysis reports A component of engineering documentation that includes calculations and analysis reports. Test plans and results A component of engineering documentation that includes test plans and results. Material lists and sourcing information A component of engineering documentation that includes material lists and sourcing information. Engineering documentation helps to communicate ideas, ensure quality and consistency, and comply with standards and regulations
6. Test
Documentation testing for engineering projects is a type of non-functional testing that ensures that a digital product’s functionality matches its documentation. It’s a part of the testing process that documents all the product’s functionality and changes.
Here are some benefits of documentation testing:
Clarity: Documentation provides transparent overviews of each team member’s work scope and objectives.
Tracking: Documentation helps track future project requirements, control test coverage, and measure testing effort.
Real-time feedback: Documentation allows developers to adjust their plans based on new feedback at any stage.
Reduced risk: Testing and commissioning can help identify and fix design or installation issues early in the project.
Documentation: Define the scope and purpose, Follow a consistent format and style, Use clear and concise language, Include relevant and sufficient details, Organize and structure your information, Review and update your test documentation
7. Installation Documents
Documentation testing is a type of non-functional testing that ensures that a digital product’s functionality matches its documentation. Test documentation includes all files that contain information about the testing team’s strategy, progress, metrics, and results.
Installation testing is a procedure that ensures that end users can install software components without any issues. It’s typically performed during the final stages of software testing. Some things that are checked during installation testing include.
Whether the application is installed in the correct folder
Whether the user can choose a default folder
Whether the installer instructions are displayed correctly
Whether the product is easy to install over the internet
Whether the software has enough disk space for the file system